本报告在参考了大量学术论文的基础上,对于干电极的制作方式,干/湿法电池的性能对比、PTFE粘接剂的应用以及干法设备进行了全面的介绍,与此同时,本报告也对干发电极的应用前景进行了详尽的分析和市场空间测算。
第一部分:干法电极技术层面深度解析
1、干法与湿法的工艺介绍及材料对比
传统湿法工艺是将活性物、导电剂、粘接剂按比例混合在溶剂中,并通过狭缝涂布模头按要求涂覆在集流体表面并辊压。
干法工艺是将活性颗粒、导电剂和进行干混均匀后加入粘接剂,在粘接剂原纤化作用下形成自支撑膜,最后辊压覆盖在集流体表面。
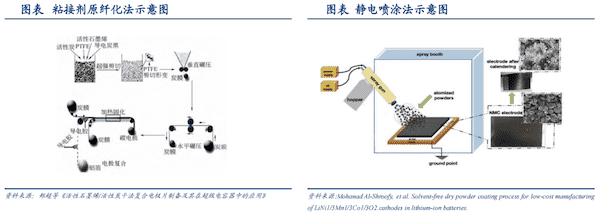
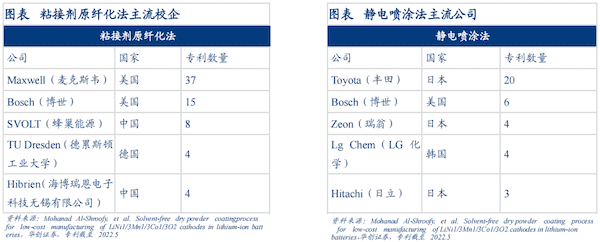
2.2、原纤化干法工艺技术原理
温度、剪切是影响 PTFE 原纤化的重要因素。当温度高于 19 度,PTFE 会从三斜晶系转变为六方晶系,分子链会变软,也是形成原纤维的主要原因。
原纤化制膜是极片辊压的前段环节,主流的原纤化制膜机器为:1)气流粉碎机;2)螺杆挤出机;3)开炼机。在 PTFE 与活性物质充分混合后,混合物被送入原纤化制膜机,在机器的辊压下混合物会形成自支撑膜。Maxwell 实验数据显示,进料速度越小,原纤化电极膜的阻抗越大;与此同时,电极膜阻抗会伴随辊压的力度增加而降低。
1、干法工艺成本更低,制造成本降低 18%
干法工艺对环境更友好,且更适配大规模生产。NMP(N-甲基吡咯烷酮)溶剂有毒,对环境不友好,且在传统湿法工艺中需要对其进行回收,会消耗大量的能量。干法工艺无需溶剂,在极片涂布环节减少烘烤及溶剂回收环节,工艺流程更简单,设备占地面积更小,更适配极片的大规模生产。
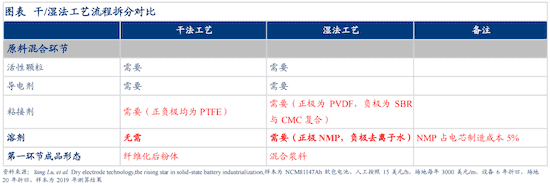
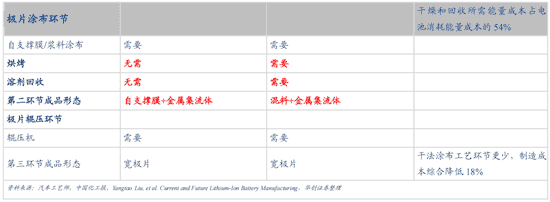
干法电极在 PTFE 原纤化的作用下,较湿法电极可以实现更加平整的形貌。由于湿法需要溶剂,在溶剂蒸发后,活性物质与导电剂之间会留出更多空隙,空隙导致材料的压实密度不高。干法不存在烘干过程,因此不存在溶剂蒸发后留下的空隙,颗粒之间的接触更为紧密。
干法电极可以做到更大的压实密度。干法条件下压实后,裂纹、微孔等问题更少。磷酸铁锂压实密度可从 2.30 g/cm3 提升至 3.05 g/cm3,提升幅度 32.61%;三元材料压实密度可从 3.34 g/cm3 提升至 3.62 g/cm3,提升幅度 8.38%。石墨负极压实密度可从 1.63 g/cm3提升至 1.81 g/com3,提升幅度 11.04%。由于单位体积下含有更多的活性物质,因此干法电极也具备实现更大能量密度的技术路径。
相同条件下,干法电池能量密度可提升 20%。根据 Maxwell 的实验数据,干法电极能量密度可以超过 300 Wh/kg,且具备实现 500 Wh/kg 的可能性。
干法电极厚度极限更大,可以提升面容量。传统湿法电极涂布厚度极限是 160 µm,而干法的厚度区间为 30 µm-5 mm。更大的厚度区间也能适配更多样的活性物质。
3、干法电池电性能更优
干法工艺电池的循环性能、耐久度和阻抗在实验室条件下均更优。由于目前还没有工业实际生产数据,故本文引用的是《锂离子电池用无溶剂干法电极的制备及其性能研究》的论文公开数据。
纤维网提升干电极的材料稳定性,进而增强电性能。湿法工艺中,在电池经历 500 圈循环后,活性颗粒内应力不断积累,导致剖面出现裂纹,最终降低了电池性能。在干法工艺下,纤维网包覆在活性材料表面,在经历 500 圈的充放电后,网状结构保持完整,颗粒表面的裂缝较少,与此同时,原纤化后的网状结构能抑制活性物质体积膨胀,防止颗粒从集流体上脱落,增强了稳定性,提高了电性能。
三、干法电极在下一代电池中的应用
1、固态电池&干电极:抛弃传统液态原材料,但均面临固固界面问题
固态电池是下一代锂电池,抛弃传统液态电解液。干法电极抛弃传统液态溶剂,与固态电池设计理念类似。在干法技术的赋能下,固态电池的极片制造过程可以实现完全干燥,消除了湿法工艺烘干后,溶剂分子的残留问题。此外,利用粘接剂的原纤化作用制造固体电解质膜,能提升固态电池性能:
成膜无溶剂,提高离子导电率
固态电解质和粘接剂干混成膜,无需烘干制造成本更低
工艺简单,更适配规模化量产
2、预锂化&干电极:不用考虑预锂材料与溶剂的兼容性,降低预锂化难度
预锂化策略用于缓解电池首周循环的锂离子损失。锂离子会与负极反应形成SEI 膜,造成 6%-15%的锂离子不可逆损失。预锂策略更偏好干燥的电极生产环境。湿法下,溶剂会与预锂添加剂产生副反应,消耗活性锂,增加电池阻抗削弱预锂效果,干法无需溶剂,干燥的生产环境更适配预锂化策略的需求。
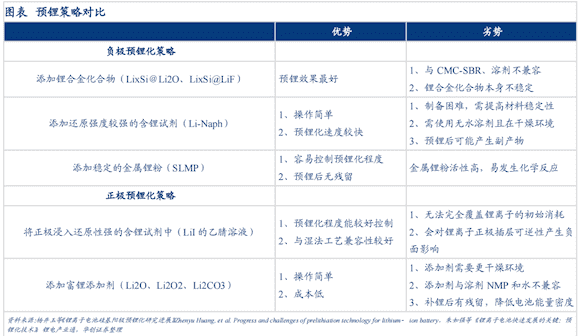
四、干法电极技术难点及综合对比
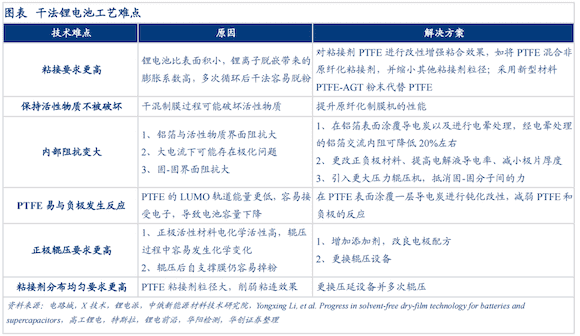
干电极工艺较传统湿法是全面的升级。在制造流程上,干电极步骤更少,制造成本及能耗更低,原料对环境友好,更适配大规模生产;在电池性能上,干法电池可以实现更高的能量密度,电池的电性能和机械性能均更优;在应用端,干法电池更适配固态电池、4680 等新一代电池的制造需求。
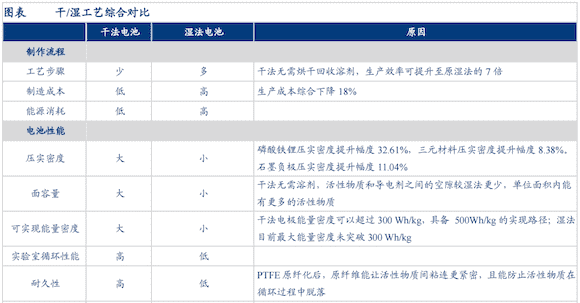
第二部分:干法电极粘结剂
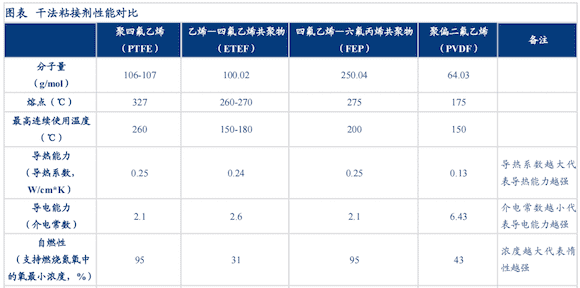
PTFE会与负极表面的锂离子反应生成氟化锂,削弱粘合效果,降低容量。单克 PTFE大约会消耗1070mAh的锂,电池中的PTFE含量越高,消耗的锂也越多。在实验中,排除首周充放电形成SEI膜的影响后,在第二次放电曲线中,PTFE含量越高放电电流越小,因此证实聚四氟乙烯会与锂离子反应,影响电池的性能。
在 PTFE 表面涂覆导电碳实现粘接剂的钝化。根据特斯拉的专利介绍,涂层材料包含电导体(导电碳、炭黑等)以及颗粒材料(粉末状碳材料)。涂层覆盖面积占 PTFE 粒子表面的 90%以上,厚度介于 0.1-100μm。
涂层有以下几方面作用:
作为导体加强活性物质导电能力
对 PTFE 表面进行改性,提高粘接剂稳定性
作为钝化材料抑制电解液等材料的分解。在 PTFE 原纤化后,涂层由于分子间的相互作用力,仍会附着在颗粒表面
2、混合非原纤化材料
原纤化后形成的自支撑膜仍会存在活性物质和粘接剂的粘连作用降低的问题,而活性物质的脱落会导致电池内部的电阻增加从而影响电池性能。
将PTFE与非原纤化材料混合提高电极膜性能。可对传统的非原纤化材料(如PVDF、CMC)研磨成为更小粒径的材料,再与 PTFE 混合形成新型的粘接剂。特斯拉专利中混合物 PVDF、CMC、PTFE 质量比为 1:1:2。更小粒径的粘接剂能实现电极膜活性物质更均匀的分布,与此同时,粒径更小的粘接剂有更强的粘连性。
三、干法电极对PTFE的需求
第三部分:干法电极加工设备
主流的自支撑膜制造设备分为气流粉碎机、螺杆挤出机以及开炼机。气流粉碎机效率最高,螺杆挤出机良率最高
气流粉碎机:压缩空气通过喷嘴高速射入粉碎腔后,活性物质及粘接剂混合物通过进料口到达粉碎腔。混合物在高压气流的作用下相互碰撞粉碎实现原纤化,最后,混合物随气流上升至分级腔在辊压设备作用下形成自支撑膜。气流粉碎机的工作效率最高。
螺杆挤出机:混料自料口进入螺杆充满螺槽后,会在旋转的螺杆作用下在料筒内壁和螺杆表面不断被压实、搅拌以及混合。在压缩段结束处,螺杆会将混合均匀的物料按要求挤出机头,在机头中混合物会被塑成电极膜并送离挤出机,螺杆挤出机的良率最高。
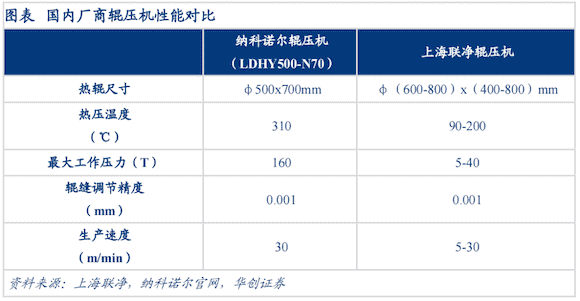
设备大型化集成化是未来发展趋势。将加料、混料、纤维化、制膜、辊压、分切、收卷等功能集成在一起,降低流转时间,提高效率及一致性等,设备价值量更高。特斯拉采用的压延切边一体机的辊压部分类似开炼机。在机器的头部放料后,混料会沿着走带方向进入辊筒,由于下游的辊筒转速快于上游,辊缝间形成的高剪切力会对活性物质、导电剂以及粘接剂挤压并混合。在原纤化作用下形成的自支撑膜会附着到下游更快的辊筒上并反复压延。机器侧边的计量辊可以控制辊筒的转速和温度,而在机器的尾部会设置分切系统,将成型的宽电极膜按要求裁切成窄电极膜。双面涂层与集流体复合层压机器是集合正/负电极膜生产、电极膜和集流体层压和极片收卷,本质是压延切边复合一体机。
压延切边一体机优势是:
提高干电极制作效率
降低极片在设备间的流转时间,减少掉粉
产品良率更好控制,提升一致性
更好检测极片的厚度、压延均匀性等指标
双面涂层与集流体复合层压机器是集合,正/负电极膜生产、电极膜和集流体层压和极片收卷,本质是压延切边复合一体机。
干法电极是较传统湿法电极的全面升级
干电极所需新型粘接剂 PTFE,市场空间巨大
【声明】本文报告内容摘录自华创证券研究报告,所引用资料版权均归原作者所有
发表评论 取消回复